
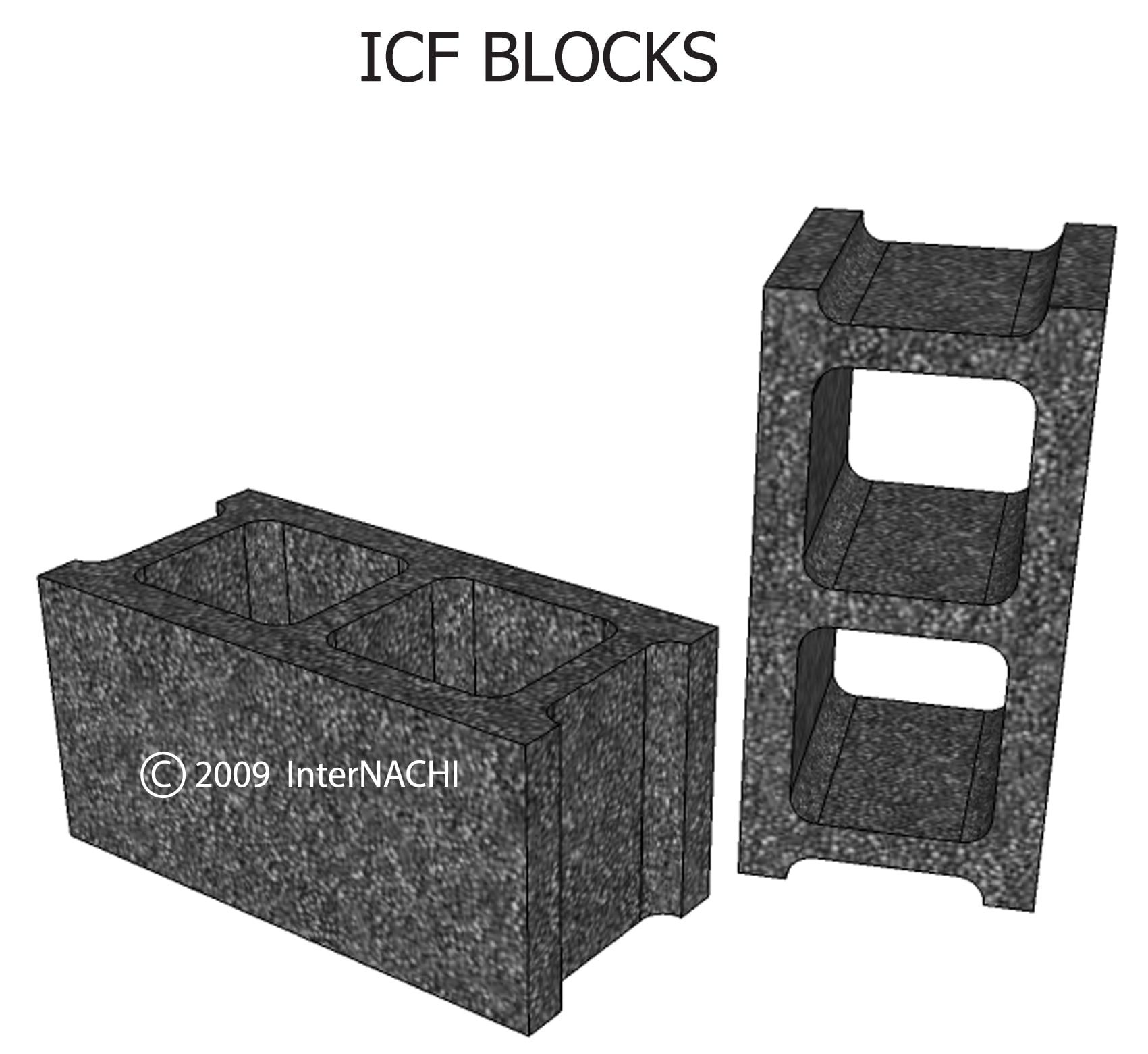
Quad-Lock Insulated Concrete Forms and LiteForm are flat panel systems using panels and ties.
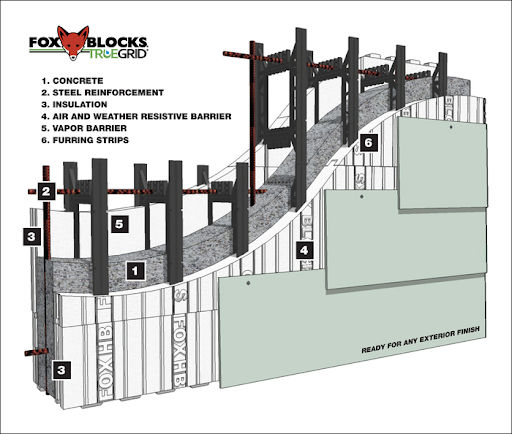
The foam panels are connected with plastic or steel ties that hold them in place. The result is a wall of uniform flat thickness similar to a conventional cast-in-place wall. Flat” or “panel” systems are similar to a conventionally poured wall.

Within ICFs there are a variety of formats. Because we are all better than wood.” Various ICF Formats As Jerry Kachlic, founder of Eco Building Systems, makers of the Perfect Block, said, “People need to be aware of all alternative building products. Here’s a rundown of the types of ICFs on the market for those who truly are getting an introduction to ICFs in this issue. “Though applications and approaches to ICF technologies differ in the marketplace, the combination of EPS foam insulation and embedded attachments deliver astounding benefits to both builders and occupants,” says Brian Corder, president and CEO of BuildBlock Building Systems. “And it does work, as long as the concrete is the right concrete and it’s done correctly.”īuilders can put ICF’s proven performance to work in many different applications across multiple markets and sectors, from pools to residential homes, mid-rise and multifamily buildings, schools, and high rise applications. “ICF has been tried and tested now, in the US and Canada for over 25 years,” says Kennaw. Today, ICFs are an accepted system within all building codes in North America. During the post-war years when plastic foams were developed, both a Canadian and Europeans developed similar blocks. In Europe around the time of World War II, blocks were made of treated wood fibers held together by cement. ICFs have a long history, and in fact were an offshoot of the original products, which is what we now consider the “alternative” ICFs.
ICF BLOCKS SIZES HOW TO
“If somebody is educated in how to work with an insulated concrete form you could pretty much build with any of them,” says Mike Kennaw, who represents the industry as chair of the board of directors of the Insulating Concrete Forms Manufacturers Association (ICFMA), and is also vice president of sales and marketing for Fox Blocks. Compare the different systems by looking at our ICF Comparison Charts: Despite these differences, each system performs more or less the same way.
ICF BLOCKS SIZES FULL
In some products, the plastic webs run the full height of the form while in others they stop short. The spacing of the plastic webs or ties, the pieces that hold the two foam panels together, could be spaced 6 inches (152 mm) on center, such as the Amvic R22 or BuildBlock, while others are spaced 8 inches (203mm) on center, such as Fox Blocks (or Amvic R30). Some are 2 inches (51 mm), some are 2-1/2 inches (63.5 mm), and some are 2-5/8 of an inch (67 mm). There are also differences in foam thicknesses. Larger systems have fewer pieces to handle but may have other disadvantages such as being heavier and costing more Block sizes are typically 16 inches high by 48 inches long, although they are also available in various sizes and shapes, such as 12 or 18 inches tall or in different shapes for radius walls. The forms can have core sizes of 4 to 12 inches, but 6 or 8 inches are the most common. Each manufacturer of ICFs makes their blocks with slight physical differences. These are forms that sandwich cast-in-place concrete between two layers of foam insulation material. ICFs stand for insulating (or insulated) concrete forms.
